Selecting Membrane Adhesives
Published: 17 March 2020
Updated: 11 October 2023
Single-ply membranes (EPDM, TPO and PVC) are supplied in both unbacked and fleece-backed varieties, each type has specific properties that affect how it can be adhered.
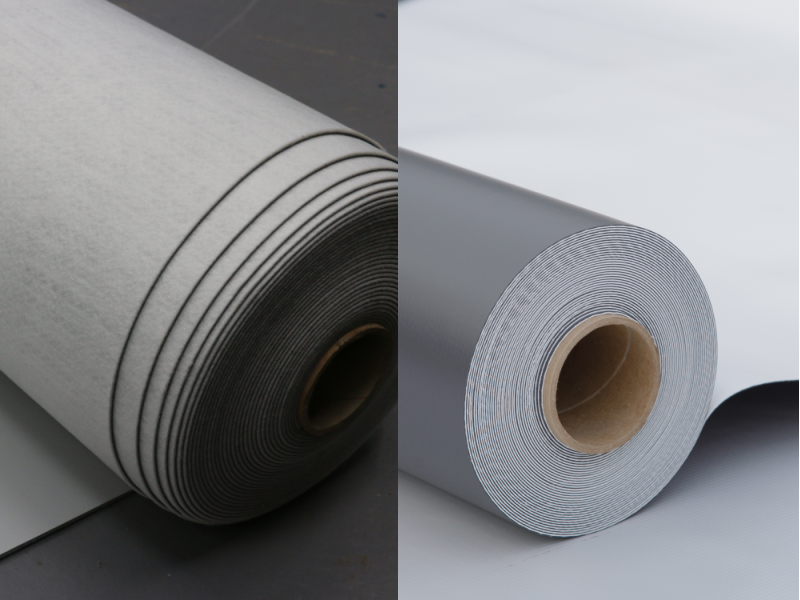
Roofing membranes form the upper layer of single-ply roofing systems, providing a watertight, aesthetically pleasing appearance and protection against the elements.
Single-ply membranes are supplied in both unbacked and fleece-backed varieties. Special care must be taken when choosing the right membrane for the job, as performance requirements and lifespan can vary for each membrane type. Securing the membranes correctly and to the manufacturer’s specification is highly important to protect the length of warranty.
Selecting Adhesives
Adhesives offer numerous benefits, in particular promoting the aesthetics of the roof and providing proven high wind up-lift ratings.
The membrane type should be evaluated first to narrow down suitable adhesive options. Membrane adhesives are developed for precise applications for specific reasons. Although single-ply membranes tend to fall into three main polymer types (EPDM, TPO and PVC), each type has specific properties that affect how it can be adhered.
It is essential that the specified grade of adhesive is used to ensure the correct level of adhesion and performance to meet the warranty of the waterproofing system. Adhesives are tested to a high standard by system manufacturers. Not using the specified adhesive risks the warranty being invalid, as well as giving unknown performance.
Membrane adhesives typically come in a variety of application methods, ranging from roller-applied to specialist spray-applied products. The complexity of the roofing project and the ease of application should also be considered when selecting an adhesive that aligns with the roofing contractor's expertise.
Membrane Types
Fleece-backed membranes
The most common method of adhering fleece-backed membranes is to use moisture-curing polyurethane adhesives. Polyurethane adhesives form tough structural bonds that resist both high and low temperature weathering, with no loss of performance for the lifetime of the warranty. These are available as solvent-free or solvent-based options, and are generally applied as a one-way stick either to the roof deck or insulation layer.
Unbacked (plain) membranes
The main polymer types of unbacked membranes are PVC, EPDM and TPO. All three types have specific properties that will affect how they can be adhered.
We work together with system suppliers to ensure the compatibility of the adhesive and membrane. It is imperative that the adhesive used has been selected by the membrane manufacturer or supplier, as these products have been tested.
Contact adhesives (applying to both membrane and substrate) are generally used for these products. Although water-based products are available for some membranes.
Membrane application tips:
- Always apply the specified coat-weight/coverage-rate evenly and ensure the correct working time is followed. This will allow for full bonding of the membrane to the substrate.
- For adhesives containing solvent, the adhesive layer must be given time to allow the solvents to evaporate to prevent entrapment in the bond line.
- Remember both temperature and relative humidity will affect the cure-rate of the adhesive. As a general rule, every 10°C increase in temperature reduces the reaction time by 50%.
- All waterproofing membranes should be fully consolidated to ensure sufficient contact. A 20kg water filled roller is recommended.
Detail areas
Once great care and attention has been used to waterproof the field areas, it is imperative that the same attention is applied to the detail areas. Securing the membrane to a vertical surface is often the most difficult and time-consuming part of installation.
Detailing adhesives are usually solvent-based contact adhesives, which are available as brush and spray grades.
Detail area application tips:
- As bonding membranes to vertical surfaces can be time-consuming, only adhere one membrane width at a time. This will ensure that the detail work can be completed within the working time of the adhesive.
- Applying the recommended coat/coverage rate to both surfaces allows the solvents to evaporate and develop tack within the working time of the adhesive.
- The bond line must be consolidated with a roller, as this is the only way to ensure the two adhesives layers are in full contact.
Find out more about our range of adhesives here, or contact us to speak with our one of dedicated Sales team.
Our infographics below summarise the key points:
You may also be interested in
Sign up to our newsletter to get our blogs delivered straight to your inbox
This form is protected by reCAPTCHA and the Google Privacy Policy and Terms of Service apply.